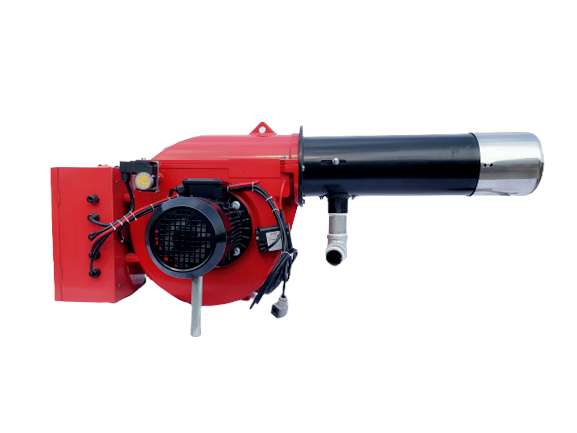
When the shut-off valve has cut off the air source and recovers the air supply, the inlet valve of the pressure regulator should be closed first. After troubleshooting, the screw cap should be unscrewed and the valve stem should be pulled out to reset the brake to jam the valve stem and install the screw. Cover, you can supply air. The natural gas burner is planned for the blast furnace exhaust gas produced by iron and steel enterprises. The blast furnace gas incinerator uses blast furnace exhaust gas with any pressure and any calorific value to perform active incineration and other functions. The natural gas incinerator is a heating device (such as boilers, industrial furnaces, etc.) that uses hot coal gas as the heat source to complete the hot coal gas incineration process. The effect is to introduce hot coal gas and combustion air into the heating equipment or burn in the burner according to a certain proportion and certain mixing conditions, and to meet the requirements of the direction, shape, rigidity and spreadability of the flame in the heating process. The hot gas incinerator developed includes two parts: the incinerator body and the incineration organization. For non-constant heating equipment (such as boilers), because the heat load is not determined and the unevenness is large, it is difficult to compulsory air distribution after the incinerator is completed. Therefore, the body structure is generally self-diffusion (or free-style), that is, the hot gas is not combined with combustion-supporting The air is mixed early (or as long as it is partially mixed when the heat intensity is high), but after being sprayed into the furnace, it is burned while being mixed with the air in the furnace.
The advantage of self-diffusion incinerators is that they are not easy to temper, have a large dispatch ratio, a simple structure, a high incineration load, and good performance; the disadvantage is a large excess air coefficient (generally 1.1-1.25) and low flame intensity. Constant temperature heating equipment (such as most closed industrial kilns), due to the high heat storage temperature in the furnace, the incineration heat load is not firm, the unevenness is small, and the gas consumption is relatively stable. Therefore, the incinerator generally chooses the premixed fractional incineration method, namely The gas and combustion air have been premixed in the incinerator or at the nozzle, and then sprayed into the furnace for incineration. The advantage of the premixed incinerator is that the air excess coefficient is small (generally 1.03~1.05) and the flame intensity is high; the disadvantage is that it is easy to temper and the dispatch ratio is small. The valve disc on the gas passage is in a "flow off" condition, and the seal is more reliable under the effect of the medium pressure. This three-way valve can be installed at both ends of the furnace close to the burner. Compared with the large four-way valve, the pipeline is shorter, which can greatly reduce the loss of pipeline when the gas is switched.